Valves are essential components in various industries, playing a crucial role in controlling the flow of fluids, gases, and other materials. They are used in plumbing, oil and gas, chemical processing, and many other sectors. This article explores the different types of valves, their applications, how to select the right valve for specific needs, and essential maintenance tips. Additionally, we will touch on the importance of integrating valves with other materials, such as geomembranes, in specific applications like environmental engineering and water management.
What are the different types of valves, and what are their primary uses?
Valves come in various types, each designed for specific applications based on the flow control required. Common types include:
- Gate Valves: Primarily used for on/off control rather than flow regulation. Suitable for applications where the valve remains fully open or fully closed.
- Ball Valves: Known for their durability and reliable sealing, they are ideal for shut-off applications and are commonly used in water and gas lines.
- Globe Valves: Used for regulating flow in pipelines. They provide excellent control and are typically used in applications where throttling is needed.
- Butterfly Valves: Lightweight and compact, butterfly valves are often used in large-diameter pipes. They are suitable for applications requiring quick shut-off.
- Check Valves: Designed to allow fluid to flow in one direction only, preventing backflow. They are essential in many systems to avoid contamination or damage.
- Needle Valves: Provide precise flow control in smaller systems. Commonly used in gas or liquid metering applications.
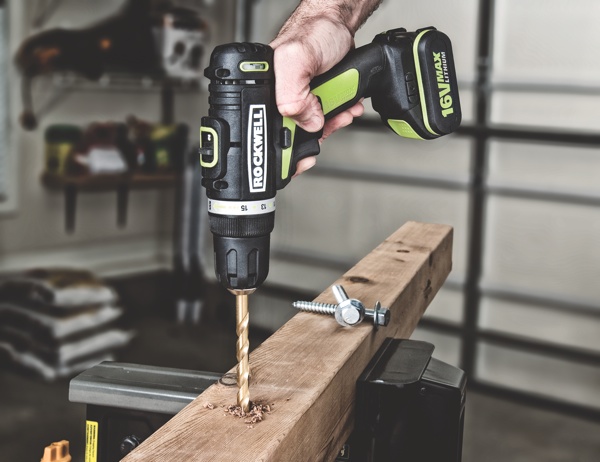
How to select the right valve for a specific application?
Selecting the right valve involves considering several factors:
- Medium: Determine whether the valve will control water, gas, oil, or chemicals. Each medium may require a different type of valve material and design.
- Pressure and Temperature: High-pressure or high-temperature applications may require valves made from specific materials like stainless steel or brass.
- Flow Control Needs: Decide if you need on/off control or if you require throttling and flow regulation. Different valves offer varying levels of control.
- Valve Size and Connection Type: Ensure the valve fits the pipe diameter and connection type (flanged, threaded, etc.) used in your system.
- Environmental Considerations: If the valve will be used in outdoor or harsh environments, it must be resistant to corrosion and weathering.
In certain applications, such as in environmental engineering, combining valves with materials like geomembranes can help control fluid flow in containment systems, landfills, or water reservoirs.
What are the common applications of valves in various industries?
Valves are widely used across multiple industries:
- Water and Wastewater Treatment: Valves control the flow and distribution of water and chemicals in treatment plants.
- Oil and Gas Industry: They are critical in controlling the flow of crude oil, natural gas, and refined products throughout the supply chain.
- Chemical Processing: Valves manage the flow of aggressive chemicals and gases under varying temperatures and pressures.
- Food and Beverage Industry: Sanitary valves are used to control the flow of liquids and gases in food processing, ensuring hygiene and safety.
- Power Generation: Valves control steam flow, cooling water, and other fluids in power plants.
- Environmental Engineering: Valves are integrated with geomembranes for applications like leachate collection in landfills or seepage control in water reservoirs.
What are the key maintenance practices to ensure the longevity of valves?
Regular maintenance of valves is essential to ensure their functionality and longevity. Key maintenance practices include:
- Routine Inspection: Regularly check for leaks, corrosion, or signs of wear and tear. Inspect valve seats, seals, and stems to ensure they are in good condition.
- Lubrication: Apply appropriate lubricants to moving parts to reduce friction and prevent wear.
- Cleaning: Keep valves clean from debris, sediment, or chemical build-up that could impede their performance.
- Pressure Testing: Periodically perform pressure tests to ensure that valves can handle the operating pressures without failing.
- Replacement of Worn Parts: Replace worn-out or damaged components, such as seals, gaskets, and seats, to prevent leaks and ensure proper sealing.
- Calibration: For valves used in critical control applications, ensure they are calibrated correctly for accurate performance.
Combining these practices with proper installation techniques, especially when integrated with materials like geomembranes, helps ensure robust and reliable fluid control systems in various industrial applications.
Valves are indispensable in numerous industries, offering crucial control over fluid and gas flow. Understanding the different types of valves, their specific applications, selection criteria, and maintenance practices can help in optimizing their performance and extending their lifespan. In applications involving environmental engineering and water management, integrating valves with materials like geomembranes provides an added layer of protection and control. Proper valve selection and maintenance are key to ensuring safe, efficient, and cost-effective operations in any industry.